ダイヤモンドライクカーボン(DLC)とは
ダイヤモンドライクカーボン(Diamond-Like Carbon, DLC)膜は,ダイヤモンドと黒鉛との中間に位置するユニークな材料である.鉄鋼材料の表面に1μmのDLCをコーティングすると,通常0.4 程度の摩擦係数が0.1 程度まで低下し,さらに削れにくくなる.またプラスチックにコーティングすると,酸素や水を通さなくなる.これらの特徴を生かして,DLC は機械材料,工具,電子機器の低摩擦・耐摩耗コーティングとして,またペットボトルのガスバリア性コーティングとして適用範囲が大きく拡大している.ものつくりにより高い環境調和性が求められる将来,DLC の適用範囲は,今後益々拡大するものと思われる.
1 はじめに
炭素材料の魅力は限りない.2010 年のノーベル物理学賞は,二次元物質グラフェンが受賞した.1996 年にはフラーレン(C60)がやはりノーベル化学賞に輝いており,炭素材料への期待の大きさを伺わせる.炭素材料には,ほかに黒鉛,カーボンナノチューブ(CNT),ダイヤモンドそしてアモルファス炭素がある.炭素は最近重要さを増している環境調和性の観点からみても,資源が多く,環境を悪化させない点で優れた材料である.物性の点でもダイヤモンドは地球上で最も高いヤング率を有し,熱伝導率も高い.CNT は鉄の20 倍の比剛性と170 倍の比強度を有すると言われている.本ヘッドラインで特集されているように,魅力的な炭素系材料を対象として,これまで多くの研究開発がなされてきている1)-4).
本稿の主役であるDLC(ダイヤモンド状炭素)は,ダイヤモンドと黒鉛の中間に位置する硬いアモルファス炭素で,ダイヤモンドのDNA と黒鉛のDNA とを合わせ持ったユニークな材料である.ここでは,コーティング材として益々重要度を増しているDLCについて合成技術と応用の観点から述べるとともに,DLCを主題とした教育の取り組みについて述べてみたい.
2 DLC とは?
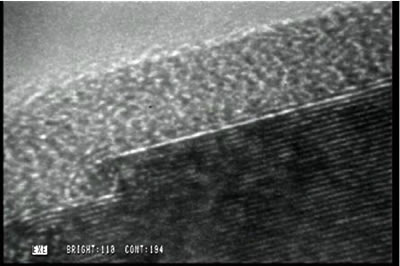
ダイヤモンドライクカーボン(Diamond-Like Carbon,以下DLC)膜は,宝石のダイヤモンドとバーベキューで使う炭の合いの子で,ダイヤモンドのsp3 結合とグラファイトのsp2 結合の両者を炭素原子の骨格構造としたアモルファス炭素膜である1)-4).DLC 中のダイヤモンド結合の成分は20~90%と幅広く,さらに水素を0-50%含むので,一言でDLC と言ってもその物性は千差万別である.そこで,DLC を何種類かに分けて産業応用をしやすくする必要に迫られており,現在DLC の標準化が検討されている.
さて,DLC はどのような組織を持つのだろうか.sp3比約40%,H 比約20atm.%のDLC のTEM 写真を図1に示す.DLCの厚さは約15nm で,マルチウォールカーボンナノチューブ(MWCNT)上にCVD 法によりアセチレンから合成したものであり,イオン加工は施していない.この写真をみると,CNT のグラフェン層がきれいに積層しているのがわかるが,DLCの領域では明確な構造がみられない.sp2結合とsp3結合がある比率で混在しているのがDLC であることは前述したが,TEMで「ここはダイヤモンド構造で,隣がグラファイト構造」といったように確認できる材料ではないアモルファス構造であることがわかる.
DLC膜は高硬度,高耐摩耗性,低摩擦係数,高絶縁性,高化学安定性,高ガスバリア性,高耐焼き付き性,高生体親和性,高赤外線透過性などの特徴を有し,表面が平坦で200℃程度の低温で合成できることから,図2 にまとめたように,電気・電子機器(ハードディスク,ビデオテープ,集積回路など)や切削工具(ドリル,エンドミル,カミソリなど),金型(光学部品,射出成形など),自動車部品(ピストンリング,カム関連部品,クラッチ板,インジェクタなど),光学部品(レンズなど), PET ボトルの酸素バリア膜,衛生機器(水栓),レンズ・窓,装飾品など幅広く応用され始めている4).とりわけ,各種硬質膜の中でも10GPa 以上の高い硬度による,優れた耐摩耗性と低い摩擦係数を有することから,機械部品の保護膜として需要が加速度的に増大している. DLC の分類と応用の関係を大まかに表1に纏めた.用途に応じたDLC 膜が上手く利用されていることがわかる.
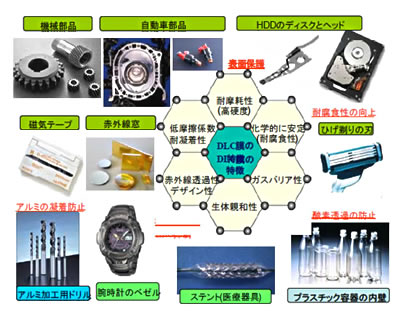
DLC の市場規模は2006 年の統計で約67.5 億円であり,年率20~30%程度で伸びていると言われている(今年度は例外的に落ち込む)が,これらは表に出ている数字であって,実際にはこの数字よりかなり大きい規模と思われる.DLC コーティングを内製で行っている企業が多いからである.さらに最近では,自動車用の量産部品としても実用化している.インジェクタ等では以前からDLC が用いられていたが,ここ5年間で適用範囲が大幅に拡大している.代表例のひとつは電磁クラッチ板へのコーティングであり5),DLC をコーティングすることにより,油中での摩擦係数がDLC コーティングにより高くなること及び滑り速度の増加により摩擦係数が増加することを利用した点でユニークな応用である.またエンジン部品としては,カムフォロワへの応用がある.これは,DOHC エンジンのカムが吸排気バルブを押す極めて重要な摺動部であって,このような箇所にDLC が実用化されたことは注目に値する6).さらにロータリーエンジンの部品にもDLC が採用されている7).これらの観点からDLC 技術は環境調和型社会の実現へのひとつのキーテクノロジーになりつつある.
ついで,ハードディスクへのDLC 応用について述べる.ハードディスクへのDLC オーバーコートは,DLC 厚さの点で他の機械的応用と一線を画する.ハードディスクは,図3 に示すように磁気メディアに書き込まれている磁気情報を浮上している磁気ヘッドにより読み取るので,出来るだけヘッドとメディアとの距離が小さいことが望まれる.従って,ヘッド及びメディアを保護しているDLC の厚さとして,最近は2nm 程度の極薄膜が要求されている.しかも,その極薄膜DLC と僅かな潤滑剤で,耐摩耗性を担保し,耐食性を持たせねばならない.
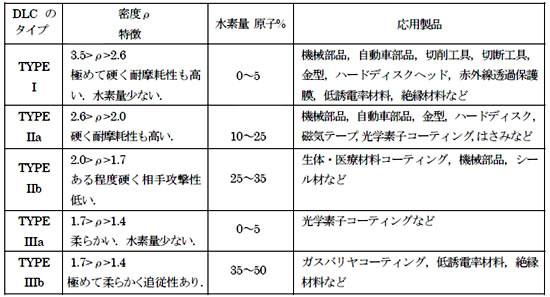
ヘッドには硬さの大きいTYPE I のDLC 膜が用いられる.また,メディアには通常TYPE IIa の膜が用いられている.TYPE I 膜のディスクへの利用が難しいのは,ドロップレットを完全に無くすことが容易でないためと言われているが,ごく最近にTYPE I の膜を利用可能との研究結果も出されている.いずれにしても,10~20 原子層厚さの膜であるから,粒子状の物質は厳禁で,しかも硬さが大きく,連続膜で高いガスバリア性を有する必要もある.DLC オーバーコートはHDDの高密度化に大きく貢献してきた.さらに進化できるかどうか,現在が正念場だ.
3 DLC の成膜方法
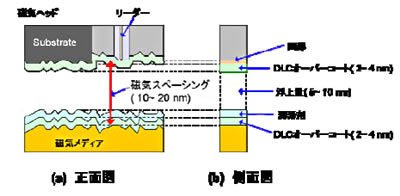
ダイヤモンド状炭素膜は,当時黎明期であったダイヤモンドの気相合成を意図したイオンビーム蒸着の実験の副産物として生まれたものである.現在でこそダイヤモンドはCVD で容易に合成されているが,1960~70 年代は,高エネルギーの炭素イオンをダイヤモンドに変換させるPVD 法が有望と思われていた観がある.ダイヤモンドが地下深くの高温超高圧状態で合成されること,隕石中にダイヤモンドが発見されたことを考えると,イオンを使うのが自然だという考えも頷ける.そんな中,1971年にAisenbergらはイオンビームによるダイヤモンドの合成実験結果をJ.Appl. Phys.に’Ion-Beam Depositionof Thin Films of Diamondlike Carbon’として発表した8).これが “Diamondlike”の使われた始めである.DLC 膜が高硬度,低摩擦係数,高耐摩耗性を有するアモルファス炭素膜として産業に応用がなされてきたのは,1980 年代後半の光学部品への耐環境性コーティングからである思われる.1990 年代にはいるとJ. Robertson のグループがDLC 膜の構造とその特性について詳細に調べ,水素がどれくらい含まれているか,ダイヤモンド成分が全体の何%あるかを調べて,光学バンドギャップ,屈折率,硬度,ヤング率,摩擦係数との関係をまとめている9).さらに機械的特性については,膜構造とヤング率,硬さとの関係について言及しており,ヤング率はダイヤモンド構造が多いと高くなり,また水素がたくさん含まれている膜では,高分子のようになってしまって膜の硬度が低下することなどを指摘している10).
DLC 膜の製造法の一例を図4 に示す4).DLC はメタンなどの含炭素気体またはグラファイトなどの固体原料から合成される.これらの原料に放電などでエネルギーを与えて炭素を含む正イオンを生成させ,このイオンを電界で加速して陰極基板上に供給することにより,基板上にDLC 膜が生成する.従って,DLC 膜の合成はイオンの必要なプロセスであると言って良い.ダイヤモンド合成が中性ラジカルプロセスであるのと対照的であり,ダイヤモンドの出来損ないがDLC の訳ではなくて,両者の合成条件は大きく異なっている.基板温度は,DLC では通常は室温~200℃で高くても500℃であり,ダイヤモンドの800℃と比較して低いのが特徴である.DLC はイオンが存在しないと生成しないが,同時に中性ラジカルやクラスターも成膜に寄与していると考えられ,基板に到達するイオンとラジカルとの比がDLC の合成速度や膜質に影響を及ぼす.
4 おわりに
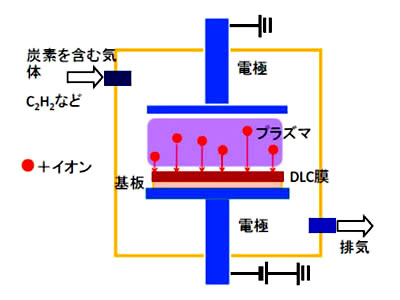
DLC の分類,合成法及び応用について述べた.多くの研究者の長い間の努力により,DLC コーティングの主要目的である低摩擦・耐摩耗性コーティング技術はかなり進み,潤滑剤とのマッチングやリコート技術も順次クリアされ,実用範囲が拡大している.今後は成膜効率の改善,さらなる高信頼化,成膜工程の単純化,有機溶剤の使用量低減などによるトータルのコーティングコストの削減,ドライ応用の展開等が求められるだろう.
今回は紹介しなかったが,DLC をコーティングすると,多くの材料に対して大気中で摩擦係数が0.1 程度まで小さくなるので,大きいCO2排出量低減効果がある11,12).電力でいえば0.40kg-CO2/kWh の排出量があるので,世の中で動いている物の摩擦係数がすべて半分になったらCO2排出量低減にどれくらい貢献があるか,容易に想像できよう.以上のように,DLC 技術は,機械の性能と安全・安心の実現及び環境調和性向上の3つの観点から機械を支えてゆく技術として今後ますます重要になってゆくものと確信される.研究者,技術者のさらなる努力に期待したい.さらに,DLC だけではなく,カーボンテクノロジーに携わる夢をもった若手を育成してゆければ本望である.
参考文献
1) A. C. Ferrari, J. Robertson: Phys. Rev.. B61,20 (2000) 14095.
2) 齋藤秀俊:DLC膜ハンドブック,NTS 出版(2006)
3) A. Erdemir: Surf. Coat. Technol., 120-121(1999) 589.
4) 大竹尚登:DLCの応用技術,シーエムシー出版(2007)
5) 太刀川英男,森 広行,中西和之,長谷川英雄,舟木義行:まてりあ,44,3(2005)245.
6) M. Kano, Y. Yasuda, Y.Mabuchi, J. Ye, S. Konishi: Transient Processes in Tribology, 43,(2004) 689
7) 中谷達行,岡本圭司,安藤 悟,鷲見智夫:ニューダイヤモンド,79(2005)36.
8) S. Aisenberg and R. Chabot: J. Appl. Phys., 42-7(1971) 2953.
9) J.Robertson, Surf. Coat. Technol., 50, 3, (1992), 185-203
10) J.Robertson, Diamond Relat. Mater., 1, 5-6, (1992), 397-406
11) 大竹尚登,大花継頼,中東孝浩,斎藤秀俊: DLC コーティングによるCO2削減効果の半定量化(1), ニューダイヤモンド, 24, (2008), 6.
12) 大竹尚登,中東孝浩,大花継頼,斎藤秀俊: DLC コーティングによるCO2削減効果の半定量化(2), ニューダイヤモンド, 25, (2009), 22.
用語解説
CVD法:Chemical Vapor Deposition の略.原料のガスを分解して基材上に薄膜を堆積させる方法.化学気相成長法とも呼ばれる.
ドロップレット:固体原料から薄膜を作製する際に,通常は原子・分子になって基材上に堆積するのに対して,ミクロン、サブミクロン単位の液滴状になって堆積した粒状物質.一般に薄膜の機械的特性を低減させる.
リコート:一度コーティングした工具などが摩耗して使えなくなったときに,廃棄せず再利用を目的として再度コーティングすること.
東京工業大学大学院理工学研究科機械物理工学専攻・教授 大竹 尚登